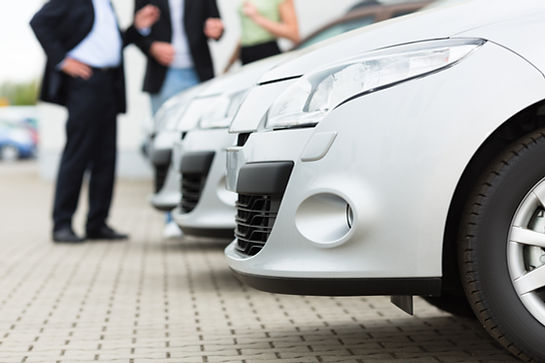
From Rags to Riches- The Toyota Way
The fabled story of the Toyota Way and the scintillating performance of the automotive company has set it a class apart from the crowd of hoi polloi. Try as you much, the Toyota Way cannot be spoon-fed to any other company. For it’s not just a tool applicable for departmental solutions, it’s an operational philosophy, nurtured and cultivated for years. Thus, while Toyota manages to expand exponentially, increase market share and keep labor costs low, without compromising on quality, juggernauts like General Motors and Ford keep spiraling down the financial staircase even after emulating The Toyota Way.
What was once declared a bankrupt company in 1950 paced the way to success through sheer discipline and the Toyota Way became the staple diet of Operations ever since. In 1960, 60 Toyota cars out of 100 sent to the US were resent for rework, earning them the infamous nickname ‘Japanese Junk’. Some odd 40 years later, Toyota reigned the US market and mastered a whopping $14 billion revenue in 2006. The secret key was kaizen, the aim for continuous improvement every day, that led the automotive giant towards jojo- a slow, gradual and steady rise.

Toyota Light Vehicles Sales in the US (1961-2015)
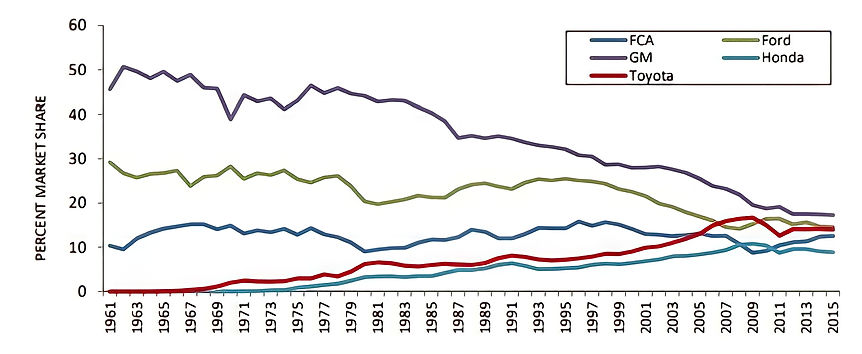
U.S. Total Vehicle Sales Market Share by Company, 1961-2015
The Toyota Mantra
The 14 principles form the gospel of Toyota production system, which was honed to perfection with sublime patience, discipline, and a culture of respect towards people.

The Toyota Way- 14 Principles
Management Decisions based on Long Term Philosophy
The automotive company emphasized on decisions based on long term philosophy, instead of short-term paychecks. Toyota’s long-term vision of delivering quality and contributing to economic growth gave purpose to the individual elements in the organization.
From Right Process to Right Results
The most important pillars of TPS are Just in Time (JIT) and Jidoka.
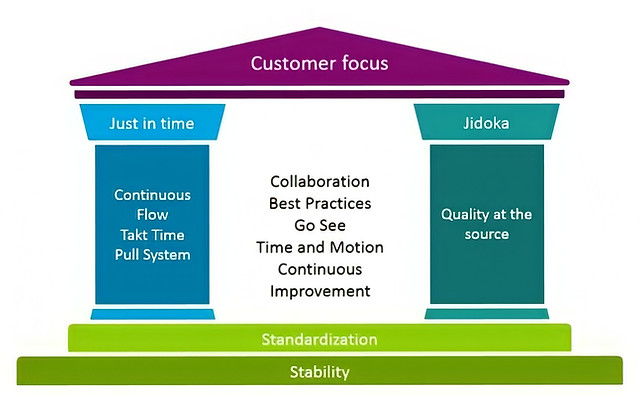
In every step of Toyota assembly line, parts were produced only when needed. A signal, Kanban, would be produced that initiated the cascade of steps. The continuous pull-based process flow ensured that the company was not losing material and financial resources due to overproduction. The concept of JIT ensured that idle time cost, inventory housing costs were also slashed off as vehicle parts were produced based on the pull or demand placed by dealers. It strived to achieve the elimination of 7 types of waste in the system- overproduction, motion, waiting (idle) time, conveyance, processing, inventory, correction or rework. The emphasis on waste reduction is well portrayed in a case study by HBR that shows how a Toyota manager went through rigorous training before assuming his responsibilities. He was assigned with the task of improving labor productivity in a group of 19 people and reducing non-value-adding steps. The changes were as subtle as repositioning the machine handle to reduce wrist strain and improve safety, relocating material stores and moving the light curtains, and those were enough to enable the group to use 15 people instead of 19.
.png)
.png)
*Processes were rated from red (worst) to green (best) depending on ergonomic parameters and risk factors
The Change in Productivity and Ergonomics of the Plant Processes after implementation of changes in the training phase at Toyota plant
In the phase of rewriting the record books for automotive manufacturing, Toyota also introduced the Andon Cord. Any employee can “pull the rope” and stop the entire production system if an error is spotted. The Japanese giant believed in flagging error signals at the very root of it and fixing the problem so that it does not get transmitted along the assembly line like a dominoes. It was a simple, but effective way to implement jidoka, a concept that aims to automate the system with a human touch. Integrating quality control at every node, stopping the workflow as soon as the most meagre problem surfaces have been instrumental in making Toyota what it is.

Toyota encouraged the culture of pulling Andon Cord whenever there was the slightest anomaly. Instead of rebuking the workers, the top team thanked the worker. Mike Rother, author of Toyota Kata, talks about how a Toyota assembly plant, staffed to handle about 1,000 Andon calls per shift became very concerned when the calls dropped to 700 per shift. Toyota found that this could only indicate that either people are not calling for help or they were experiencing fewer problems.
Toyota’s philosophy is rooted in quality control and solving problems at the root, which encourages employees to see the problem for themselves. If the quality of parts outsourced from suppliers did not match the expected level, Toyota would take up the responsibility to personally investigate the supplier site and drill down to every process to eliminate the defect. In 2003, Toyota collaborated with an Athens plant, Chassisco for its Suprima model. When the problem erupted, and the company’s reputation was at the verge of being scathed, Toyota sent engineers to the site in-person to examine for themselves where the defects stemmed from.
Nurturing Values in the Organization
Toyota believed in harnessing a high level of emotional connect among the employees and create a warm culture at work. Emphasis was laid on respecting people, the team and all the stakeholders of the chain, including vendors and suppliers, and also ensuring that workload was evenly distributed.
While focusing on lowering supply costs, Toyota did not impose cost-cutting demands on its suppliers, unlike the other players. Instead, they helped their supplier reduce internal scrap from 20% to 2%, thus sowing the seed for a healthy long-term relation. Another instance can be cited referring to the $800 million Toyota facility in Texas. The firm faced a fiasco over assembling the Tundra. As the suppliers were far off and the extra distance might pose quality issues, Toyota built an on-site supplier park to accommodate 21 suppliers. The Japanese automobile firm strengthened the relation with its suppliers both in the pre-launch and post-launch phase and nurtured a healthy collaboration aiming for continuous improvement.
Striving for Perfection
Toyota embraces the idea of problem-solving through detailed understanding, stable and unified decisions and rapid implementation. That ensures the company’s path towards achieving maximum efficiency through continuous improvement, kaizen.
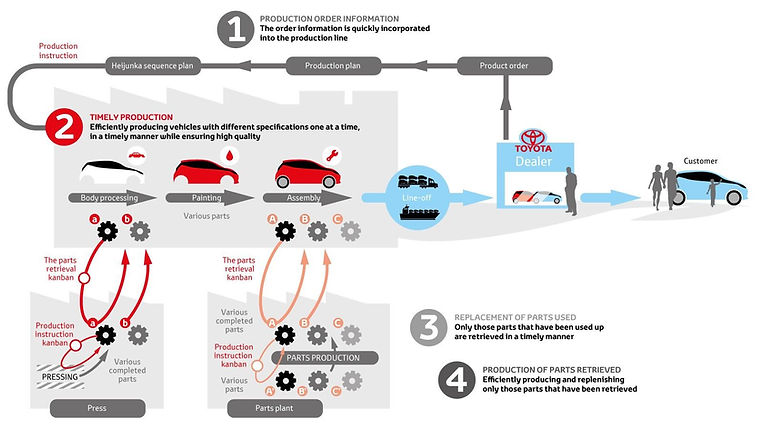
The Toyota Production System- A Schematic Layout
(Still) Learning
From a company where workers would turn up drunk, or not at all, Toyota positioned itself as one of the leading car manufacturers of the world. Leaving behind the horrors of the World War, Japan prides itself on companies as successful as Toyota for reigning the globe in their domains. The success of the company is attributed to its culture and philosophy, where learning and improvement are the constant objectives.